Retrofitting Balconies: Lessons from the Field
What we’ve learnt post-Grenfell
Responding to a changing landscape in building safety
The tragic events at Grenfell Tower in 2017 marked a watershed moment for the construction industry. In the years since, the Building Safety Act and Dame Judith Hackitt’s independent review have fundamentally changed how balcony structures are assessed, designed, and retrofitted. At AliDeck, we’ve worked closely with contractors, developers, and housing associations across the UK and Ireland to deliver safe, compliant aluminium balcony systems that address urgent remediation needs.
As new guidance continues to emerge, retrofitting has become one of the most pressing and complex challenges facing building owners. The combination of resident safety, regulatory compliance, and practical site constraints means that one-size-fits-all solutions no longer apply.
How post-Grenfell reforms are reshaping retrofit practices
The Hackitt report called for a systemic shift in how buildings are built and maintained — and that’s exactly what the Building Safety Regulator (BSR) is now enforcing. For balconies, this means full non-combustible systems, robust drainage, clear record-keeping, and traceability of materials. Aluminium systems like ours — Class A fire-rated and Made in Britain — offer clarity and compliance from day one.
However, retrofitting isn’t just about meeting legislation. It’s about long-term resilience. Timber and composite materials, which once passed as acceptable, are now considered high-risk. For occupied buildings, this has prompted urgent remediation work. But every site presents different constraints — from building age and original design limitations to logistical challenges like access and delivery.
Navigating challenging retrofit sites
Older developments rarely come with straightforward retrofit access. Many have limited lifting options, inconsistent floor levels, or narrow walkways that make standard installations difficult. Over the years, we’ve been involved in hundreds of such projects, and one thing remains true — early collaboration between contractor, architect, and supplier reduces costly delays.
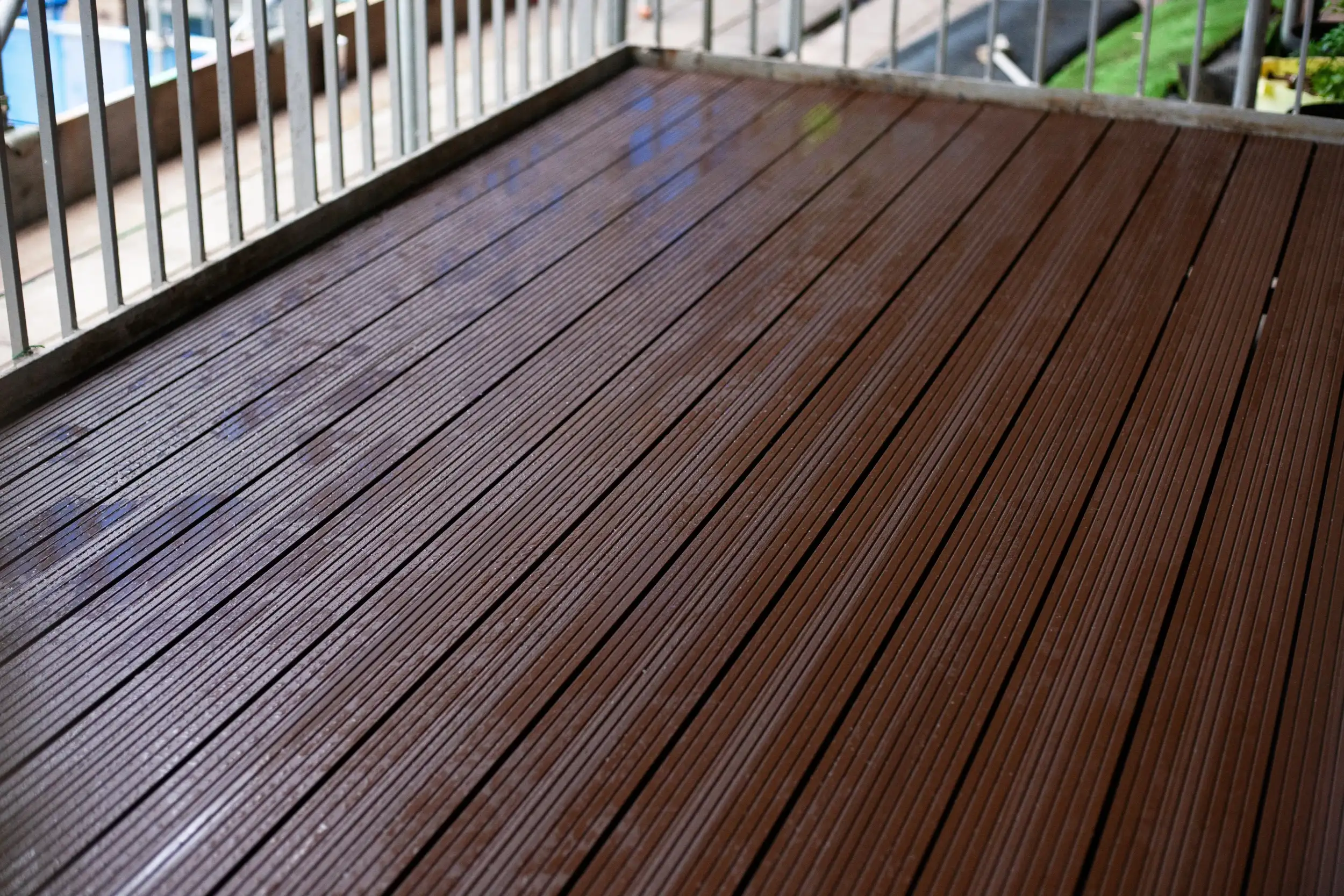
On one remediation project in Hackney, for example, we were contracted to supply XL decking and drainage solutions to replace combustible materials on 11 existing balconies. In addition to product specification, we supported the contractor (BMA) with delivery planning, powder-coating to match design intent, and installation training. The result was a seamless process, a compliant result, and a safer environment for residents.
We also help customers deal with challenges such as:
- Working on live sites without disturbing residents by splitting up deliveries
- Minimising structural disruption when retrofitting existing balconies
- Matching the look of old materials with new aluminium finishes
Supporting the sector with retrofit-ready systems
AliDeck’s modular decking, soffit, and drainage systems are ideally suited for retrofit projects. Lightweight, fully fire-rated, and easy to install, our solutions reduce on-site time while helping customers meet the requirements of the BSR and fire engineers.
We understand that time is critical. With lead times as short as three weeks and everything powder-coated in-house and extruded in the UK, we help projects stay on track. Our team regularly visits sites for design consultations, material take-offs, and bespoke training to ensure no detail is missed.
Ready to discuss your next retrofit project? Contact our team on 01622 534050 or email info@alideck.co.uk